Common Problems and Troubleshooting Tips for Industrial Reciprocating Compressors
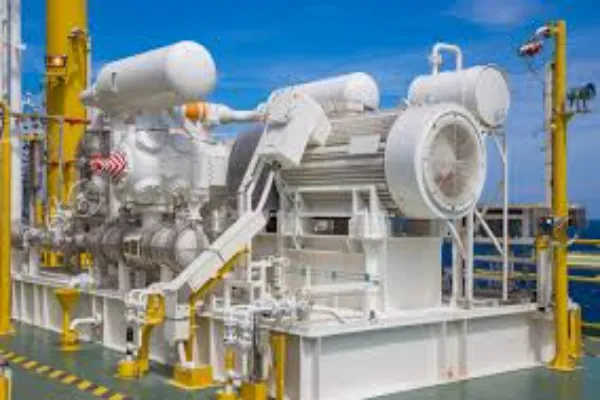
In the demanding world of industrial environments, the reliability and efficiency of machinery play pivotal roles. Among these essential machines, industrial reciprocating compressors stand out for their critical function in various applications, from refining to power generation industries. However, like all complex systems, they are not immune to operational challenges and breakdowns, which can substantially impact productivity and safety. Understanding the common problems and mastering the troubleshooting techniques can significantly mitigate these risks. Read to discover how to address and resolve the typical issues plaguing these indispensable industry workhorses.
Understanding Reciprocating Compressor Failures: Key Challenges in Industrial Settings
Industrial reciprocating compressors central to industrial applications such as natural gas processing and power generation industries confront various operational challenges. The unique design of these compressors, characterized by the cyclic movement of the piston within a cylinder, demands precise management of internal components to ensure reliability and efficiency. Failures often come down to wear and tear on these components, especially under the high pressure and extreme conditions typical of refining and process gas handling.
One common issue involves the deterioration of the discharge valve, a critical part ensuring the correct flow of compressed gas into the storage tank or system. If the discharge valve fails to open or close properly, it can lead to inefficiency, increased energy consumption, and eventual breakdown due to the fluctuating internal gas pressure. Similarly, problems can arise from the piston rod and cylinder, where uneven wear, inadequate lubrication, or damage can impair the reciprocating motion, leading to leaks or catastrophic failure.
Regular maintenance and monitoring cannot be overstated in extending the lifespan of industrial reciprocating compressors. Observing changes in the duty cycle, ensuring the integrity of the compressor frame, and adjusting clearance volume to maintain optimal suction pressure are vital steps. By addressing these areas, industries can mitigate risks associated with high operational stresses, safeguarding against unexpected downtime and promoting greater safety and productivity.
Efficient Maintenance Practices: Resolving Common Issues in Industrial Reciprocating Compressors
Maintaining the operational integrity of industrial reciprocating compressors involves a keen understanding of their unique demands and implementing preventative maintenance practices. Regularly inspecting the compressor’s key components such as the cylinder, piston rod, and discharge valve helps identify early signs of wear and potential failures. This proactive approach is essential in preventing the deterioration of these critical parts and ensuring the compressor’s reliability in demanding industrial settings.
Proper lubrication is pivotal in reciprocating compressors’ smooth operation and longevity. Ensuring the piston rod and cylinder are adequately lubricated reduces friction, a common cause of overheating and component failure. Attention to this detail can prevent significant downtime and repair costs, highlighting the importance of integrating lubrication checks into the compressor’s maintenance schedule.
Adjusting the clearance volume and monitoring the suction pressure are crucial steps in troubleshooting issues related to efficiency drops or abnormal operating conditions. By fine-tuning the clearance volume, operators can optimize the compressor’s performance, catering to the application’s specific needs, whether in refining processes or natural gas handling. These adjustments and careful monitoring of suction pressure enable smoother operation and enhance the compressor’s duty cycle, contributing to overall system efficiency and reliability.
Optimizing Performance: Proven Troubleshooting Strategies for Industrial Reciprocating Compressor Operations
In demanding refining and power generation environments, optimizing the performance of industrial reciprocating compressors is non-negotiable. A key strategy involves monitoring the dual-acting design, which allows compression on both piston sides during a single cycle portion. This design significantly boosts efficiency but requires meticulous attention to gas pressure and temperature management to prevent operational imbalances.
Another critical troubleshooting approach targets the modular design, particularly the distance piece and clearance pocket. These components play vital roles in managing gas pressure and ensuring the safety and integrity of the compressor frame. Regular inspection and adjustment prevent the accumulation of contaminants and ensure the compressor functions within its optimal performance parameters, thus maintaining reliability and extending the cycle.
Lastly, addressing issues with the intercooler, an essential component for reducing the temperature of the compressed gas between stages, is crucial. An efficiently functioning intercooler directly impacts the overall thermal efficiency of the reciprocating air compressor, contributing to lower operating costs and improved system reliability. Ensuring it is free from blockages and operating at the correct capacity can mitigate many performance issues, fostering smoother operation and greater safety in industrial settings.
Overall, mastering the troubleshooting techniques for industrial reciprocating compressors is crucial for ensuring uninterrupted operations and maximizing productivity in demanding industrial environments. By understanding common problems and implementing efficient maintenance practices, industries can enhance these indispensable machines’ reliability, efficiency, and safety, ultimately safeguarding their critical roles in various industrial applications.